Your cart is currently empty!
Special Supplying Quick Couplings for Hydraulic and Pneumatic system
AKJia specializes in manufacturing and supplying high-quality quick couplings for pneumatic and hydraulic systems. With decades of expertise and a strong commitment to precision engineering, we offer a full range of quick connect and disconnect couplings designed to suit a wide variety of industries and applications — including agriculture, construction, automotive, manufacturing, and industrial automation.
From ISO A and ISO B hydraulic quick couplings to push-to-connect pneumatic fittings and flat face couplers, we deliver reliable solutions that ensure leak-free, efficient, and safe connections. Whether you’re looking for standard couplings or customized options, AKJia is your one-stop source for durable, high-performance quick couplings at competitive prices.
Explore our collection and find the right connection — fast, easy, and trusted by professionals worldwide.
Quick Couplings by ISO Standard
To help you quickly find the right products for your system, we’ve organized our quick couplings by internationally recognized ISO standards. These standards define key dimensions, performance requirements, and interchangeability, ensuring compatibility and safety across a wide range of equipment and applications.
While many of our quick couplings are designed according to ISO standards, not all types of quick connectors have official international standards. In such cases, we follow widely accepted interchange standards based on the designs of well-known manufacturers. These are commonly referred to as brand interchange couplings — for example, “Parker 6600 Series interchange” or “ARO 210 Interchange.”
These non-ISO standard couplings are engineered to match the critical dimensions and performance of the original manufacturer’s design, ensuring full compatibility across systems.
Quick Couplings by Connection Method
Quick couplings can be categorized not only by standards but also by how they connect and disconnect. Different applications require different mechanisms for ease of use, pressure handling, safety, and durability. At AKJia, we offer a wide range of connection styles to meet your specific operational needs.
Quick Couplings by Applications
At AKJia, we understand that different industries have unique demands when it comes to fluid and air connections. That’s why we offer a wide range of quick couplings tailored for specific applications — ensuring optimal performance, safety, and compatibility in every environment.
Whether you’re working in agriculture, construction machinery, industrial automation, pneumatic tools, hydraulic equipment, or material handling systems, we have the right coupling solution for your job.
Quick Couplings by Features
Choosing the right quick coupling often depends on specific functional requirements. At AKJia, we provide a diverse selection of quick couplings designed with specialized features to meet demanding conditions, improve safety, and enhance performance.
Whether you need to prevent fluid leakage, connect under residual pressure, or simplify complex multi-line connections, our feature-based categories help you find the ideal solution:
Quick Couplings by Materials
The choice of body material plays a critical role in the durability, corrosion resistance, and overall performance of quick couplings in different environments. At AKJia, we offer quick couplings made from a variety of materials to meet the needs of specific applications — from general-purpose use to harsh, corrosive, or high-pressure conditions.
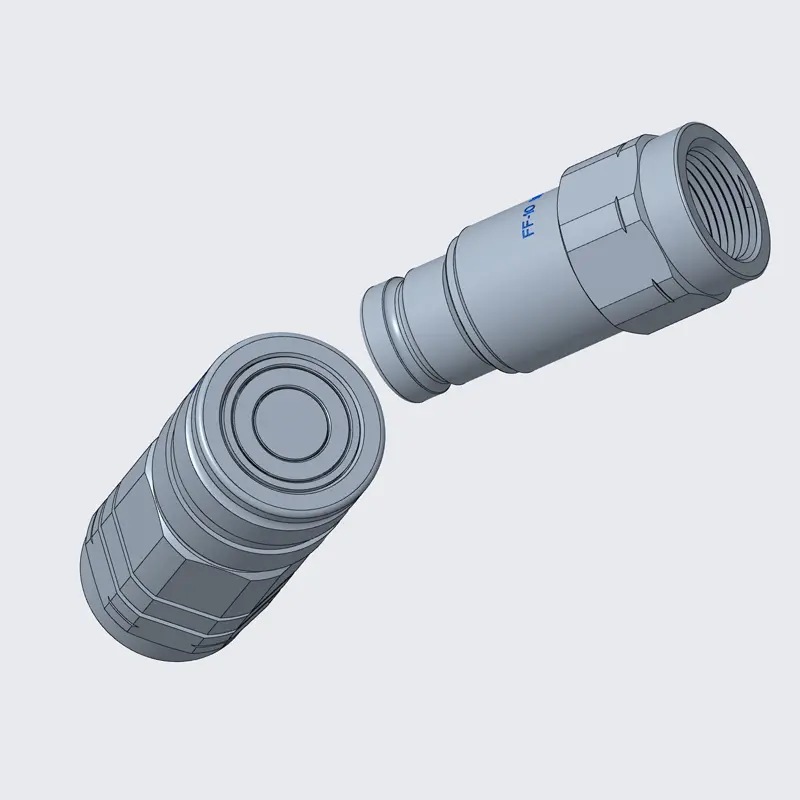
Aluminum
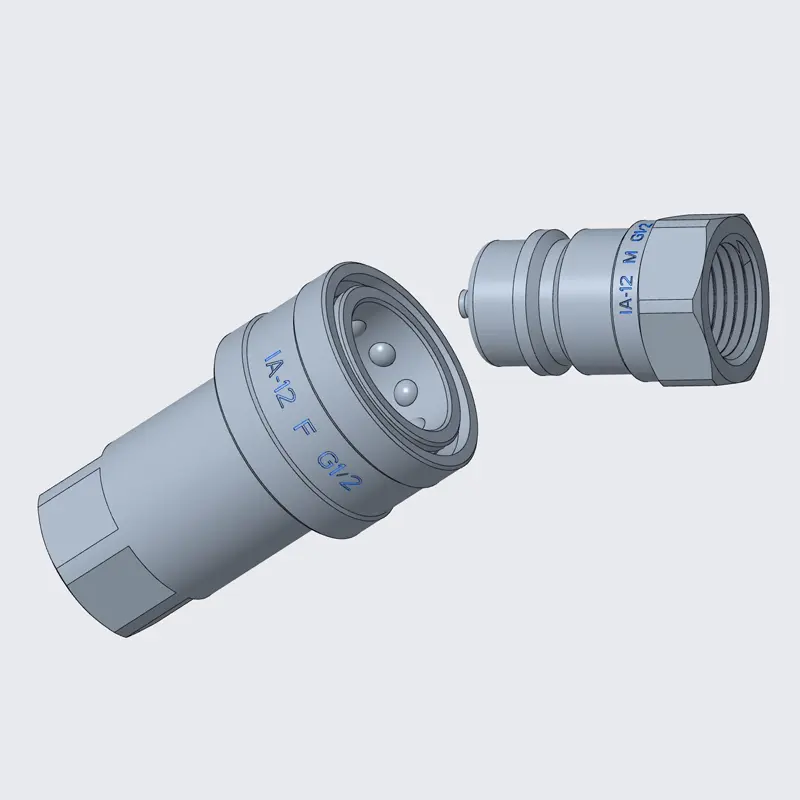
Plastic / Composite
How to buy correct quick coupling
For the vast majority of quick coupling purchasers, their typical need is to replace damaged or aging quick couplings on their current equipment. They can identify compatible replacements based on known specifications such as ISO standards, connection types, application environments, functional requirements, material compositions, or thread parameters. Our website’s menu system allows users to navigate through categorized listings and apply detailed filters to locate interchangeable products.
When selecting quick couplings for product design, critical application parameters must guide the decision-making process:
Material Selection Based on Fluid Media
Different fluids require specific coupling materials and seal compounds, with cost considerations playing a significant role. Our material compatibility chart (available for download) assists in proper selection, though direct consultation is recommended for complex applications.
Our production focuses on metallic couplings using:
- Primary materials: Carbon steel, stainless steel, brass
- Specialty options: Aluminum alloys, tool steels
- Seal materials feature specialized elastomers with distinct performance characteristics:
- Common: Nitrile (NBR), Fluorocarbon (FKM)
- Specialized: EPDM, Neoprene (CR)
- Premium: Perfluoroelastomer (FFKM) for extreme conditions
Pressure Rating Considerations
In most hydraulic circuit applications, the choice of working pressure and burst pressure needs to be carefully considered. However, many quick coupling users have a common misconception that products of the same standard have identical design working pressures. While the working pressure can be found in international standards such as ISO 7241, this only represents the minimum requirement set by the standard. In reality, due to differences in design among manufacturers, the actual working pressure can vary. Typically, a manufacturer’s specified working pressure is higher than the standard requirement.
For safety considerations, manufacturers typically set the working pressure at about 1/4 to 1/3 of the burst pressure and conduct 10,000 cycles of pressure testing to verify it. In practice, the actual working pressure can be increased by 10%-15% above the rated value. As a result, many genuine manufacturers specify a working pressure that exceeds the minimum requirement set by ISO standards. Operating at a slightly higher pressure does not compromise the service life of the quick coupling.
Additionally, working pressure varies depending on the application and testing conditions. Some applications, such as agricultural machinery, involve frequent pressure fluctuations, whereas others, like hydraulic jacks, have a more stable pressure output. Because of these differences, the pressure testing methods for these applications differ, leading to significant variations in the rated working pressure even for couplings made from the same material (e.g., carbon steel).
However, if the operating environment changes, a quick coupling originally rated for a higher working pressure may no longer meet the requirements in a different application. For example, a quick coupling rated for 720 bar in a hydraulic jack application may only be suitable for 350-400 bar in agricultural and forestry machinery. Therefore, when selecting a quick coupling, users should not rely solely on the working pressure rating. It is essential to consult the manufacturer to ensure compatibility with the intended application.